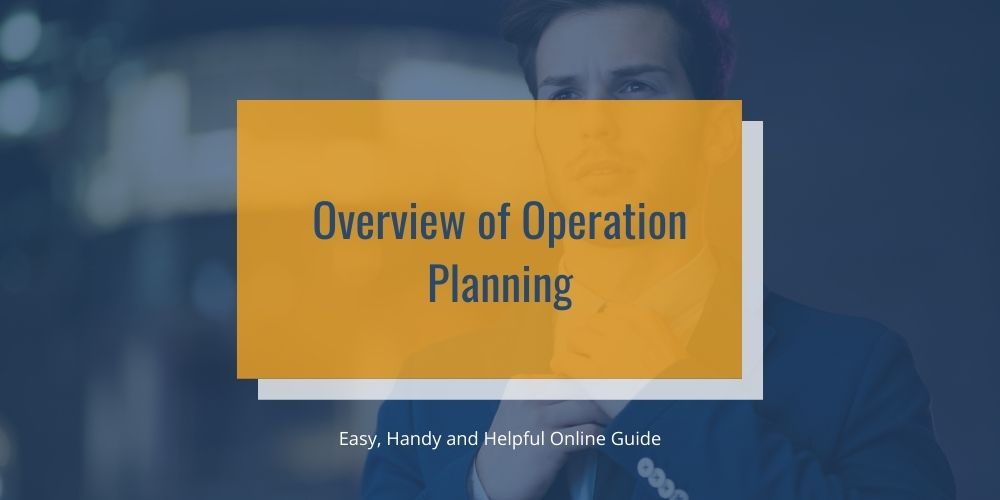
What is Operational Planning?
Operational planning requires identifying and detailing the measures that individuals can take to support the executive management team’s plans and priorities. An operating plan is highly thorough, outlining the who, what, where, and when involved in the management of the company’s everyday tasks and low-level operations. The tactical plan is assisted by this kind of plan, which is more of a mid-level plan.
The schedule itself has to follow certain requirements in order to qualify as an operations plan. The first condition is that, along with tactical and strategic strategies, the strategy exists. These other two plans are accompanied by an operating plan which includes further information about how an organization and its team members can accomplish the objectives defined in the high-level plans.
They need to ensure that supporting management team members have a clear understanding of what they need to do to facilitate the accomplishment of the priorities identified as executive management members develop the operational and strategic plans. Providing the information contained in an operating plan will provide a better sense of their duties to representatives of supportive management.
Only a single region or department of a company should be protected by an operations plan. Usually, if the strategy is too broad, it will not get into the level of detail required to highlight how those procedures and processes will be accomplished. For example, if an operating plan was produced by a manufacturing company, it might outline a strategy for each of the goods it produces or for each of the plants it operates.
When a company or organization draws from a company-wide business strategy and brings it under a microscope, organizational preparation is what happens. It is future-oriented: it sets out department budgets and objectives to propel the strategic plan’s progress for the next 1-3 years with specific, team-based activities.
When a whole group buys-in, setting due dates for projects, calculating targets for success, reporting on challenges, and collaborating efficiently, organizational strategies work best. When there is coordination across departments, they work much better to ensure that the whole machine is running smoothly as each team hits its benchmark.
What Are the Benefits of Operational Planning?
Every strategy has a major impact on all concerned team members, and some of those can be to the advantage or to the detriment of your business. It’s best to find out as soon as possible if it’s to their detriment, so you can change your organizational strategy and pivot quickly.
That is the whole point of operational planning: in real-time, or at any benchmark, you get to see the impact of the activities on the business’s bottom line, so you know exactly when to pivot. And you know exactly when things go wrong and why with a strategy that is as customary for each department as an operating plan.
How to develop an operational plan
As operational plans are designed in an attempt to allocate money, resources, and personnel for each cycle of 1-3 years, this effort should ideally be served by all the measures that an operational plan needs to include.
Who Manages the Operational Plan?
Typically, the operating plan is handled by middle management, while the strategic plan is implemented from the top down. In addition, its reach is limited and can vary with the focus on mapping out regular tasks on an annual basis.
The operating plan is ideally set out and executed by many middle managers because it requires the consideration of day-to-day operations, resources, and tasks.
Also Read: What are the different Levels of Management?
Examples of Operation Planning
There are several types of examples for the plan of operations. We have included a condensed version below for the analysis.
- Project of Manufacturing Plant Operations
- Objective: Boost workflow for plants
- Category: Prepare for Single-Use
- Needed resources: Education, performance research, and new equipment that works quickly and more effectively
- Tasks: learning how to set up new equipment, finding ways to minimize waste from manufacturing, deciding how best to reduce the amount of inventory kept in the factory, and identifying techniques for improving material handling processes.
A company may outline its short-term, divisional, or departmental goals and identify the strategies needed to achieve those goals by developing an organizational plan. Operations plans work along with other kinds of business plans to define an organization’s strategic objectives as well as how the company plans to accomplish these goals.
Purpose of an Operational Plan
Understanding the difference between an “operational plan” and a “strategic plan” is significant. The strategic plan is about setting the organization’s course, establishing priorities and goals, and defining a variety of tactics to be followed so that the organization can achieve its objectives. The strategic plan is a general roadmap for the organization’s management according to stakeholders’ goals and objectives. The strategic plan DOES NOT define the day-to-day operations and responsibilities involved in operating the company.
On the other hand, the DOES Organizational Plan offers extremely precise information explicitly to guide individuals to perform the requisite day-to-day activities in the functioning of the company. In carrying out their daily work, corporate management and personnel can constantly refer to the operating plan. What, who, when, and how much is set out in the Operating Plan:
The methods and activities that need to be done
- Who – the people who are responsible for and of the tactics and tasks?
- When – The deadlines for the completion of strategies/tasks
- How much – the sum of financial support provided for each strategy/task to be completed