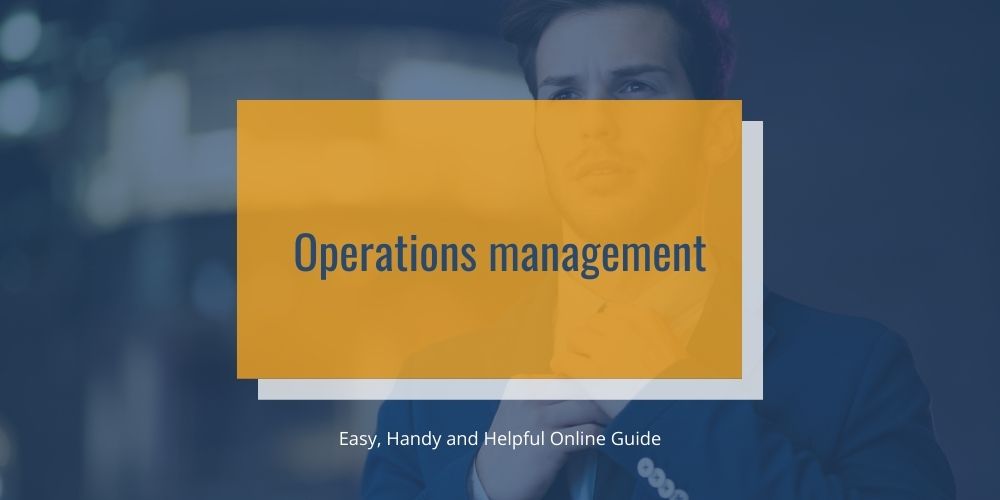
Meaning of Operations management
Operations management is the management of operational processes within a company to create the highest degree of productivity possible. To optimize an organization’s benefit, it is concerned with turning materials and energy into products and services as effectively as possible. To reach the optimum net profit margin achievable, operations management teams aim to balance costs with sales.
Defining Operations Management
Management of operations includes the use of personnel, supplies, facilities, and technological tools. Based on the requirements of consumers and the capacity of the company, operations managers tend to purchase, produce and then distribute products to customers.
Operations management deals with various strategic concerns, including calculating the scale of production plants and methods of project management and applying the information technology network structure. Management of sales volumes, namely work-in-process concentrations and procurement of raw materials, quality control, handling of materials, and machine maintenance, is another functional concern.
Management of operations involves researching the use of raw materials and ensuring that no waste occurs. Operations managers use various formulas to decide when and how big an inventory order is to be handled and how much inventory is to be held on hand, such as the economic order quantity formula.
Functions of Operations Management
- A vital operations management function relates to inventory control across the production process. To be an efficient professional in operations management, one must be able to comprehend the processes that are important to what a business does and make them flow and work together smoothly. Thorough knowledge of logistics includes the teamwork involved in setting up business processes in an effective way.
- A specialist in operations management recognizes local and global patterns, consumer demand, and the production of available resources. In a prompt, cost-effective way to meet consumer needs, operations management approaches the procurement of resources and the use of labor. To ensure excessive amounts are on hand, inventory levels are tracked. Operations management has to identify suppliers that supply the right products at fair prices and have the capacity to produce the product when necessary.
- Operations administrators are involved, when re-evaluating existing systems, in organizing and designing new processes. Two main factors of becoming an operations manager are organization and efficiency, and the position also demands flexibility and creativity.
Importance of Operations Management
To claim that all facets of an organization depend on the management of operations is no exaggeration. It has the potential to prepare, direct and facilitate the development of products and services. Operations managers must be able to work consistently and constructively to increase profits, which are the primary factors of company survival, to be able to survive in an ever-changing market.
Customer service, product and service efficiency, proper functional methodologies, market competition, technical innovations, and profitability can be affected by operations management. Failure to handle the activities of the company would cause substantial losses for the company.
10 Principles of Operations Management
Operations Management’s ten principles include the following:
- Fact
Operations management, rather than just the methods, need to concentrate on the overall problem. This is because a universal approach would not be able to present any instrument in itself.
- Organization
All about the operation is integrated within a manufacturing plant. All of these components have to be predictable and consistent. The operation would not be able to produce a profit result without it.
- Humility
The process of trial and error is incredibly expensive, which is why executives need to recognize that they have shortcomings. This will save cash and effort and, in the long run, help output.
- Performance
While there are different meanings of what success can be within your manufacturing plant, your client’s interest should always be taken into account. You have to keep your clients happy and come back if you want to be profitable.
- Accountability
Being responsible is essential to operate a production operation. Managers are supposed to be able to set rules and metrics while also checking whether these expectations are being met regularly. Responsibility is a must.
- Causality
Conditions are somewhat similar to the symptoms in which there are typically root factors of these two things. You will have to eradicate the root trigger to rid yourself of the issue permanently.
- Shift
Change is nice occasionally. It is important to change things with new theories and solutions available for manufacturing operations. This will ensure that stability is managed in the long run.
- Customer collaboration
Knowing what consumers are purchasing and using. This will give you a detailed understanding of what you can do to strengthen your brand and coordinate development families accordingly.
- Knowing the market
Analyzing the rivals is important. Understand their clients, processes, products, and competitive advantage in every shape.
- Quality Management
Quality control within a production operation is critical. Your consumers may be unhappy with the product you are developing without quality control. You have to use the best products, technologies, and partners for a reliable and durable product.